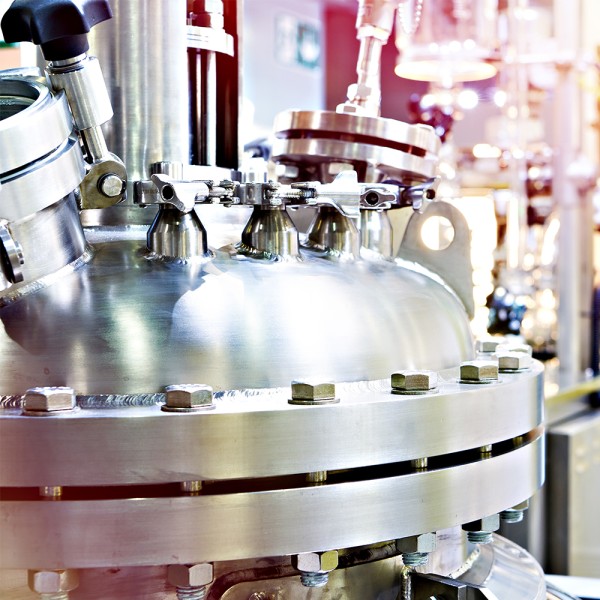
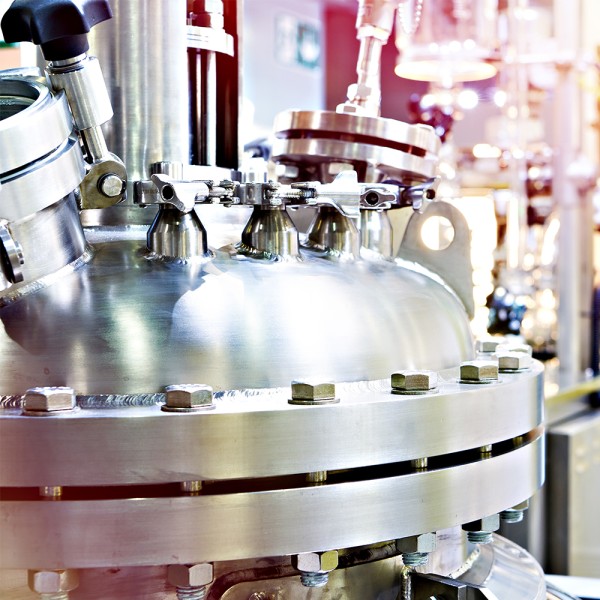
A high pressure autoclave reactor is a machine used to perform industrial and scientific procedures requiring elevated temperature and pressure. Autoclaves are used in the chemical industry to cure coatings, vulcanize rubber, and perform hydrothermal synthesis before surgical procedures. Industrial autoclaves used for a variety of industrial applications, most notably the production of composites.
A Reactor uses high pressure and temperature to perform chemical reactions or sterilize items. It employs extremely high pressures and temperatures to obtain efficient and effective results. An autoclave is designed to operate at extremely high pressures, often ranging from 50 to 350 bars. Because of the high pressure, it can generate extremely high temperatures, which are required for chemical reactions or sterilization operations. A reactor is typically used for chemical reactions such as hydrogenation, oxidation, alkylation, chlorination, carboxylation, nitration, polymerization, amination, bromination, ethoxylation, esterification, sulphonation, and other chemical reactions.
A high pressure reactor's structure comprises a cylindrical lateral shell with a traditional Tori spherical/ Ellipsoidal dish at the upper ends. The reactor's outer side contains a jacket for heating. A high pressure reactor's structure comprises a cylindrical lateral shell with a traditional Tori spherical/ Ellipsoidal dish at the upper ends. Stiffener Rings on the surface between the shell and the jacket allow regular heating or cooling media exchange and boost the vessel's strength. A autoclave performs chemical reactions or sterilization procedures due to the high pressure and temperature it produces. The equipment or tools that require sterilities or coating are placed into the reactor, and the chemicals are needed for the reaction. High pressure and temperature in sterilization operations break down the molecules in the equipment, killing any germs present. When it is pressured, the temperature rises, causing the chemical reaction to begin and continue until it is completed. The high temperature also ensures that any germs or microbes that survive sterilization are destroyed.
• Single-Stage High Pressure Autoclave Reactor - This is the most basic form. It is a single- pressure container used in sterilizing treatments.
• Two-Stage High Pressure Autoclave Reactor: This type of autoclave is more advanced than a single-stage reactor. It comprises two pressure vessels, one high-pressure and one low-pressure. The high-pressure vessel produces high pressure and temperature, whereas the low-pressure vessel is utilized to perform the chemical reaction or sterilization procedure.
The autoclave has an automatically locking detachable lid lock with a safety interlock. The unit is composed entirely of stainless steel, is heated electrically by internal heating elements, and is PID controlled for exact regulation. Two solenoid-coupled circulating air blowers keep the temperature equal.
An autoclave sterilizes equipment and other objects using steam in the medical industry. This means that all bacteria, viruses, fungi, and spores have been rendered inactive.
Autoclaves are used in education, research, biomedical research, pharmaceutical research, industrial sterilizing lab tools, glassware, culture media, and liquid media. In these situations, where efficiency, ease of use, and flexibility are valued, research-grade autoclaves are increasingly being used.
The autoclave is used in laboratories, pilot plants, and small-scale manufacturing of fine and specialty chemicals, mass drug (API) medical technologies, dyes, intermediate products, protective coatings, oils, agribusiness, petrochemical products, oil & gas, chemical engineering colleges, research institutes, defense organizations, and so on.
Pressure and temperature impact the chemical structure of the substrates, causing them to carbonize. Thus, a long biological process, such as the creation of lignite or coke, is replicated briefly. This method is very appealing for treating sludge from wastewater treatment plants. The high-temperature influence and resulting pressure treatment remove all contaminants from severely contaminated sewage sludge. By separating the sludge into its chemical components, it is disinfected. As a result, virtually sterile wastewater is produced, and HTC coal may be utilized as a soil conditioner. The high-pressure autoclave's application domains are still being exhausted.
A autoclave's high pressure and temperature allow it to carry out chemical reactions or sterilization operations. The sterilized items are placed into the reactor, together with the chemicals needed for the reaction. High pressure and temperature in sterilization operations break down the molecules in the sterilized products, killing any germs present. When it is pressured, the temperature rises, causing the chemical reaction to begin and continue until it is completed. The high temperature also ensures that any germs or microbes that survive sterilization are destroyed.
These high-pressure reactors operate at tremendous pressure and temperature, posing a severe risk to anybody nearby or working on the equipment. Before beginning any work on an autoclave, ensure that you have received the necessary training. Inside the reactor, sparks can be created, resulting in a fire. Make sure a Class-I electrical system is installed and take the steps needed to minimize sparking. The researchers should use the safety gear and avoid skipping it. A fire extinguisher must be kept handy.
Shilpa enterprises are well-known for supplying and manufacturing quality products at reasonable prices. Our crew is among the best in the chemical sector, with over ten years of experience. We offer product customization on demand to satisfy the needs of our customers. We are skilled at meeting worldwide quality requirements because we have a specialist QA staff. Our reactor can carry out a variety of operations, ranging from organic to chemical reactions, with the added benefit of working at extremely high pressures and temperatures. We welcome both large and small orders. Our professionals are available to clients 24 x 7 a week to provide product knowledge and help. Working with us ensures your contentment. Our products are packaged in class 4 shockproof packaging and can be shipped worldwide. Contact us via our contact page if you want to purchase or learn more about our products.